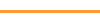
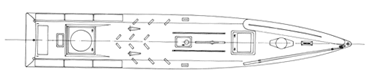
Architecte :
Guy Saillard (Ploemeur)
Longueur hors tout :
7,80 m
Longueur à la flottaison :
6,80 m Maître
bau :
1,30 m
Bau à la flottaison :
1,14 m
Epaisseur max. :
0,75 m
Tirant d'eau :
1,05 m
Poids en charge :
approx. 500-550 kg
Matériau :
flotteur en sandwich carbone-airex-époxy,
cloisons intérieures en nid d'abeille
Batteries :
12V / 120 AH
Panneaux solaires :
12V / 120 W
Dessalinisateur :
Power survivor 12V / 5 litres/h
Téléphone :
Iridium fixe et portable (fournisseurs officels :
E.T.N.A. et TDCom)
Positionneur :
GPS Furuno GP 50 Mark 2
Radio :
VHF Icom IC GM 1500 |
 |
Crédit photo :
Odyssée du vent 2003 |
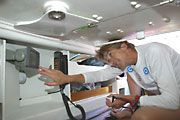 |
Réf. GMR
3381 - Photo Gilles Martin-Raget |
|
Gréements :
fournisseur officiel Neil Pryde, 6 voiles lattées
en monofilm tramé (voiles de série
RAFJET modifiées), de 4 surfaces 4,2 à
7,4 m2; 4 mâts en carbone et 3 wishbones
aluminium
Alimentation :
fournisseur officiel Best Foods Knorr
Bivouac, aliments déshydratés, lyophilisés,
fruits secs, barres énergétiques...
Chantier :
J.P.K. Composites (Larmor-Plage) en 2001,
Sailing Concept (La Ciotat) en 2002-2003.
|
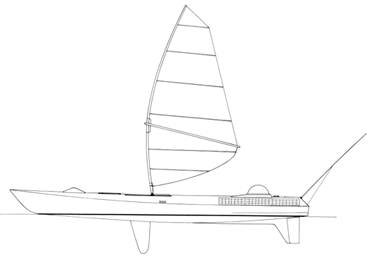
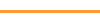
La nouvelle planche, plus légère
et plus rapide que celle que Raphaëla avait utilisée
pour sa traversée de l’Atlantique, a été
construite durant l’été 2001 sur
des plans élaborés par Guy Saillard (Architecte
Naval et Expert Maritime). La construction du flotteur
s’est faite sur le chantier de JPK Composites
à Larmor Plage.
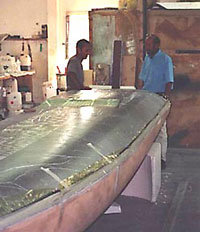 |
Réf. P0013 - Photo R.
le Gouvello |
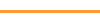
 |
Photo H. André |
Quelle personne mieux que Guy Saillard
peut nous parler de SA PLANCHE !
Guy, quels sont les principaux
impératifs fixés pour construire une planche
de "haute mer" ?
Le principal impératif
est d'être autonome, c'est-à-dire pouvoir
vivre à bord de la planche en indépendance,
ne pas dépendre de la présence ou de l'accompagnement
aléatoire d'un autre bateau qui procure une fausse
sécurité.
La planche de Raphaëla est un bouchon destiné
à flotter en toutes circonstances si le flotteur
venait à être abîmé (même
s'il est construit en sandwich mousse carbone/kevlar
/epoxy).
Il est évident que la planche doit être
également très résistante et la
plus légère possible .
Combien de temps a duré
la construction ?
La construction du flotteur proprement
dit a débuté en juillet 2001 pour se terminer
en septembre 2001.
L'équipement a été installé
entre octobre 2001 et fin mai 2002 ; il aura fallu
presque un an de mise au point pour tout installer !
Tout travail à l'intérieur de la planche
est à la fois minutieux et difficile, car tout
est très petit et il n'est pas facile de travailler
dans des espaces aussi étroits.
On a de nouveau travaillé sur la planche en 2003,
notamment pour installer le système airbag, en
partenariat avec l’ESA.
Tu as dessiné et fait
construire la planche à voile avec laquelle Stéphane
Peyron a traversé l'Atlantique en 1987, planche
sur laquelle Raphaëla a réussi 13 ans
plus tard son Défi Atlantique... quelles sont
les principales évolutions apportées sur
cette nouvelle planche ?
La principale évolution
est une recherche encore plus poussée de légèreté,
avec l’utilisation de cloisons en nid d'abeille.
La planche a également une forme plus fine à
l'avant pour mieux passer les vagues, et plus plate
à l'arrière pour mieux surfer.
Le circuit de commande de gouvernail est beaucoup plus
sophistiqué avec la fabrication et l'ajustage
de secteurs de barre qui pèsent 350 grammes
et permettent l'utilisation de drosses en kevlar.
Tout cela pour éviter à Raphaëla
les soucis qu'elle a connus avec le vieux matériel
de la transat précédente.
Et puis j’ajoute que le système airbag
développé en partenariat avec l’ESA
est une véritable innovation technologique.
Peux-tu nous parler de ce
système d’airbag ?
Après la première
tentative de Raphaëla en Méditerranée
qui s’est soldé par un chavirement et des
difficultés de redressement, et l’expérience
réussie ensuite de la traversée Marseille-Tunis,
nous avons décidé de doubler toutes les
procédures de sécurité.
Surtout que sur le Pacifique,
Raphaëla s’embarque sur une route très
peu fréquentée par d’autres
bateaux.
Elle est capable de redresser son flotteur seule
s’il chavire, mais il vaut mieux prévoir
le pire.
Nous avons donc développé avec l’ESA
un système d’airbag pour l’aider
à redresser son flotteur en cas de chavirement
et de difficultés au redressement.
Ce système d’urgence pourra se déclencher
de l’intérieur ou de l’extérieur
de la cabine.
L’airbag replié à l’arrière
du flotteur se déploiera immédiatement
et mettra donc le flotteur à l’envers
en déséquilibre. |
|
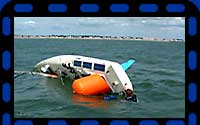 |
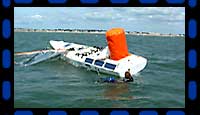 |
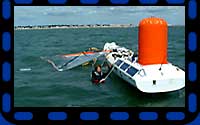 |
Coll. perso Raphaëla
le Gouvello |
|
Le redressement
du flotteur se produira alors spontanément.
Ensuite, Raphaëla pourra dégonfler son airbag,
réamorcer le système à nouveau
pour une autre fois.
Le déploiement de l’airbag s’effectue
par le biais d’un gonfleur électrique ou,
pour une procédure plus urgente, avec une cartouche
pyrotechnique spécialement conçue par
les ingénieurs de SEVA Technologies qui travaillent
étroitement avec l’ESA.
Le partenariat avec l’ESA nous a donc permis d’avoir
accès à ces technologies de pointe de
conception et de déclenchement des airbags.
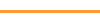

|